Candles and room diffusers have become significant market players, and it’s crucial to stay informed about the ever-evolving regulatory landscape surrounding them. Let’s explore the specific regulations that need our attention and discuss effective strategies for introducing these products to the market.
Check out this non-exhaustive overview of regulatory insights for candles and room diffusers. For a more specific study of your products, do not hesitate to reach out.
PCN Notification and UFI Code of Hazardous Mixtures: An Introduction
The CLP Regulation 1272/2008, which governs the classification, labelling, and packaging of substances and mixtures, is the key regulatory framework for these products. This regulation introduces an electronic system designed to promptly inform poison control centres about the risks associated with specific substances or mixtures. This rapid information sharing enables immediate responses to health emergencies.
At the heart of this system is the Poison Center Notification (PCN). PCN notifications are standardised transmissions detailing the composition of mixtures. These notifications must be submitted to the European Chemicals Agency (ECHA) in a specified format and include the Unique Formula Identifier (UFI) code. The UFI is a 16-digit alphanumeric code that must be displayed on the product’s label or nearby. This code is crucial in the notification process as it directly links the product to the medical professionals addressing the related health issue.
Furthermore, Article 45 of the CLP mandates the establishment of designated bodies responsible for receiving and managing information related to health emergency responses.
The Previous Notification System Under Article 45
Originally, the obligations of Article 45 centred around developing preventive measures to address medical needs, especially in health emergencies. This system was primarily used to gather information on products introduced to the market by companies and to establish poison control centres (CAVs). These centres were intended to provide medical advice during health emergencies.
However, the Article 45 notification system had several shortcomings:
The system was not harmonised across the European Union. This lack of uniformity meant that a company distributing a product in multiple EU countries faced the obligation to notify each country separately. Moreover, each country required different pieces of information, complicating the process for companies. They struggled to understand where and what information to submit for each product. For instance, in Italy, notifications had to be made to the Dangerous Preparations archive of the ISS (Istituto Superiore della Sanità), in Germany to the BfR (Bundesinstitut für Risikobewertung / German Federal Institute for Risk Assessment), in France to the French National Products and Composition Database (B.N.P.C.) and the French Poison and Toxicovigilance Centre Network (Synapse), among others.
This disjointed approach created significant challenges for companies trying to comply with regulations in different EU member states, highlighting the need for a more streamlined and harmonised system across the European Union.
Regulation 542/2017 and Its Amendments: Streamlining Hazardous Mixtures Notification
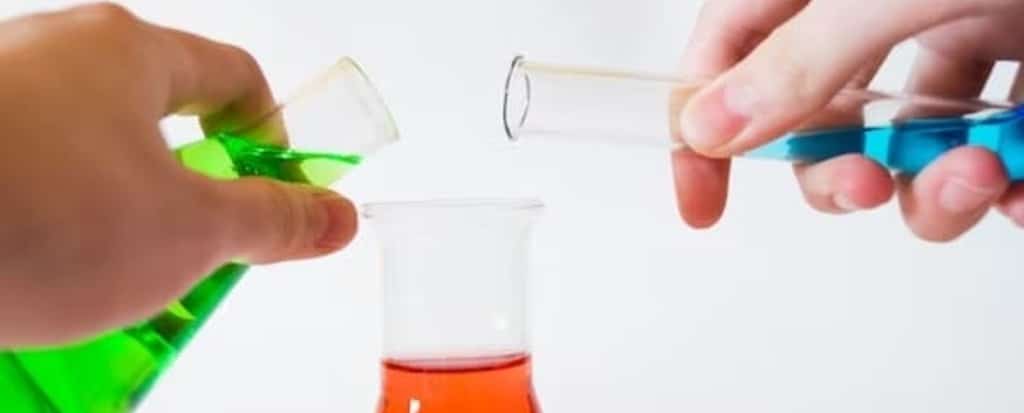
Regulation 542/2017, which amends Annex VII of the CLP, brought significant changes to enhance the safety and efficiency of hazardous mixtures notification. These changes include:
- Introduction of a New Poison Center Notification Format: This new format aims to standardise notifications across the EU, simplifying the process for companies operating in multiple member states.
- Introduction of the Unique Formulation Identifier (UFI): From 2025, it will be mandatory for all products containing dangerous mixtures to display the UFI on their labels. This 16-digit alphanumeric code is essential for quick identification in emergency situations, allowing for a rapid response.
- Modifications to the Poison Center Notification Process
Since its inception, Regulation 542/2017 has undergone two key amendments to further refine the notification process:
- The first amendment, Regulation 11/2020, postponed the implementation date of the UFI code. This delay was intended to provide companies with additional time to adapt to the new requirements.
- The second amendment, Regulation 1677/2020, introduced several innovations. These include the introduction of the concept of CIG, special concessions for bespoke paints, and other measures aimed at streamlining the notification procedure.
Implementation Timeline for Regulation 542/2017
Regulation 542/2017 applies as follows:
- For new blends for consumer and professional use: from January 1, 2021.
- For mixtures for industrial use: from January 1, 2024.
Mixtures previously notified under older national systems, like ISS in Italy, can utilise a transitional period until January 1, 2025. However, if any changes in formulation or physical properties impacting the mixture’s final classification occur after January 1, 2021, a new notification in line with Annex VIII is required, along with the assignment of a UFI. Additionally, assigning a UFI voluntarily is an option for mixtures not mandated to do so.
Notification and UFI Code Affixation Responsibilities
Under the updated system, manufacturers, importers, formulators, and relabelers are required to notify and affix the UFI code before their products enter the market. This marks a change from the previous system, where notifications could be made up to 30 days after market placement. Distributors involved in storage and resale are exempt from this notification requirement, but they play a crucial role in CLP compliance, ensuring effective information exchange throughout the supply chain.
Scope of UFI Code and PCN Notification Applicability
The UFI code and PCN mandatory notification requirements apply to mixtures classified as hazardous due to their physical and health effects, as detailed in their Material Safety Data Sheets (MSDS). This includes products like detergents, biocides, air diffusers, scented candles, and similar items.
Impact of the New System on Non-European Suppliers
Non-European suppliers are also required to comply with the above-mentioned regulations to introduce their products into the EU market. Key steps include:
- Appointing a Legal Entity responsible for notification and creation of the UFI code.
- Providing detailed information to the importer for notification purposes, including as accurate a formulation of the mixture as possible.
It’s important to note that there are specific tolerances for recording concentration ranges of each substance. These tolerances are particularly stringent for substances with certain hazards and/or at low concentrations. Therefore, it’s advisable to thoroughly discuss these details with non-EU suppliers before proceeding with deliveries.
Submission Portal for PCN Notifications
Since April 2019, PCN notifications must be submitted through the ECHA Submission Portal, a dedicated platform managed by the European Chemicals Agency (ECHA). This portal is continuously updated to accommodate the evolving requirements of PCN notifications.
What Information Is Required to Be Submitted for the PCN Notification
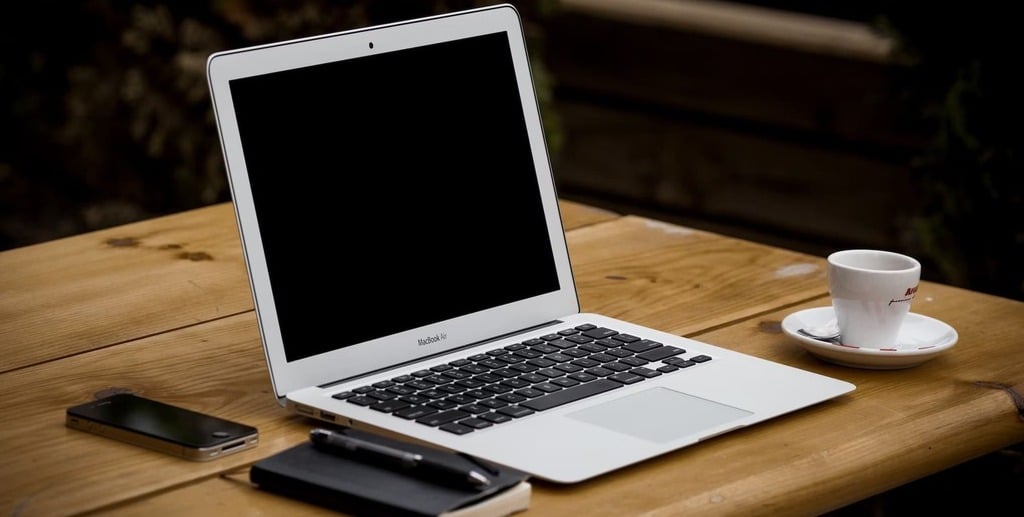
Since April 2019, PCN notifications must be submitted through the ECHA Submission Portal, a dedicated platform managed by the European Chemicals Agency (ECHA). This portal is continuously updated to accommodate the evolving requirements of PCN notifications.
The portal asks you to enter 2 types of information:
1 – PRODUCT INFORMATION
- Trade name (indicate if there is more than one and the name in other languages)
- The safety data sheet (which must contain in section 9 the data relating to the colour and physical state (if solid indicate the shape, e.g. granular, crystalline, powder, etc.)
- Type of packaging (if they are different, they will have to be indicated)
- The amount of product contained in each package
- Type of use (consumer, professional, industrial)
- Indicate the use code or the type of product (e.g. European product categorisation system – EuPCS)
2 – MIXTURE INFORMATION
- Name of the mixture
- Country of placing on the market
- Contact persons
- pH (if not available, please provide one of the justifications for not having the information)
- Report section 11 of the SDS in all languages of the selected countries
- Composition (Substances, MiM, ICG)
- UFI Code
Requirements for Candles and Scented Candles

From a chemical point of view, candles are considered “mixtures” on a support (the wick). As a result, candles fall within the scope of the Classification, Labelling and Packaging (CLP) legislation and the corresponding legislation for UFI codes and PCN notification.
Candles consist mainly of non-hazardous wax that does not need to be graded. Candles usually contain scented and coloured additives, some of which can be dangerous. If present in sufficiently high concentrations, warnings or pictograms may be required.
Guidelines for Candle Manufacturers
When marketing candles with claimed specific effects, it is advisable to provide evidentiary support confirming these effects. Additionally, safety aspects, such as labelling and product safety, should be carefully considered. Although there are no mandatory regulations specifically for candle manufacturers in this context, adherence to certain standards is recommended as a precautionary measure rather than an obligation.
- NBN EN 15426:2018 – Test relating to the emission of soot from candles
- NBN EN 15493:2019 – Fire Safety Test: flame height, combustion test, etc.
- NBN EN 15494:2019 – Safety Labels
Overview of the Registration Process Through Our Support
The registration process we offer involves several steps, each with its own lead time. Here’s a breakdown:
- MSDS Creation: We begin by creating a Material Safety Data Sheet (MSDS) based on the product’s composition. You can send us the formulation, and we’ll handle the rest. The lead time for this step is 10 business days.
- Label Advising: Using the MSDS, we provide guidance on labelling, including necessary modifications to the artworks. It’s important to note that these artworks, in the official language of the market where the candle is sold, should include the address and phone number, net weight, and any allergens present. The lead time for this is 5 business days.
- UFI Number Creation: This number is typically obtained by the importer in the EU market or the Responsible Person.
- Notification to Poison Notification Centers: The final step is notifying the appropriate poison notification centres, with a lead time of 5 business days.
Required Documents for Each Registration Step
or a smooth registration process, the following documents are needed at each stage:
- Product Formula: Provide the formula of the product along with the MSDS of every component if you wish to obtain an MSDS through our services. For fragrances or complex components, their MSDS should include their own UFI number.
- UFI Number: This is required for the registration process.
- Artworks of the Finished Product: We need these for review, ensuring they meet the necessary labelling requirements.
- Technical Information on Vegetable Wax: Obtain a technical sheet detailing possible impurities in the vegetable wax used in your product.
- Test Recommendations: While not mandatory, tests following non-mandatory standards and norms are highly recommended. (see above for details)
- Market and Packaging Details: We need to know the countries where the products will be placed, along with every net weight and type of packaging used.
A Quick Overview for France
The AFNOR Certification
Before a candle can be marketed, it should pass a series of tests in order to comply with various standards, particularly with regard to soot emission, fire safety, wick quality, labelling and combustion, as we have detailed. For example, during its combustion, a candle can emit various substances and particles that can be harmful (such as dioxins or polycyclic aromatic hydrocarbons). In France, the AFNOR group has translated these various standards, in particular the one relating to the fire safety of candles. It requires specific labelling, corresponding to the European standard EN 15494, which consists of pictograms, to be placed on the safety label and on the packaging.
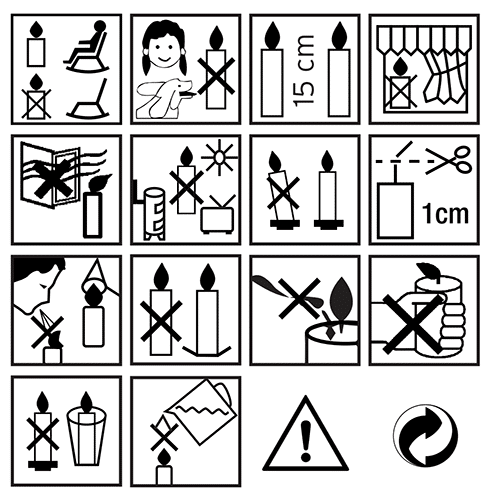
Registration Process for Room Fragrance: Steps and Lead Times
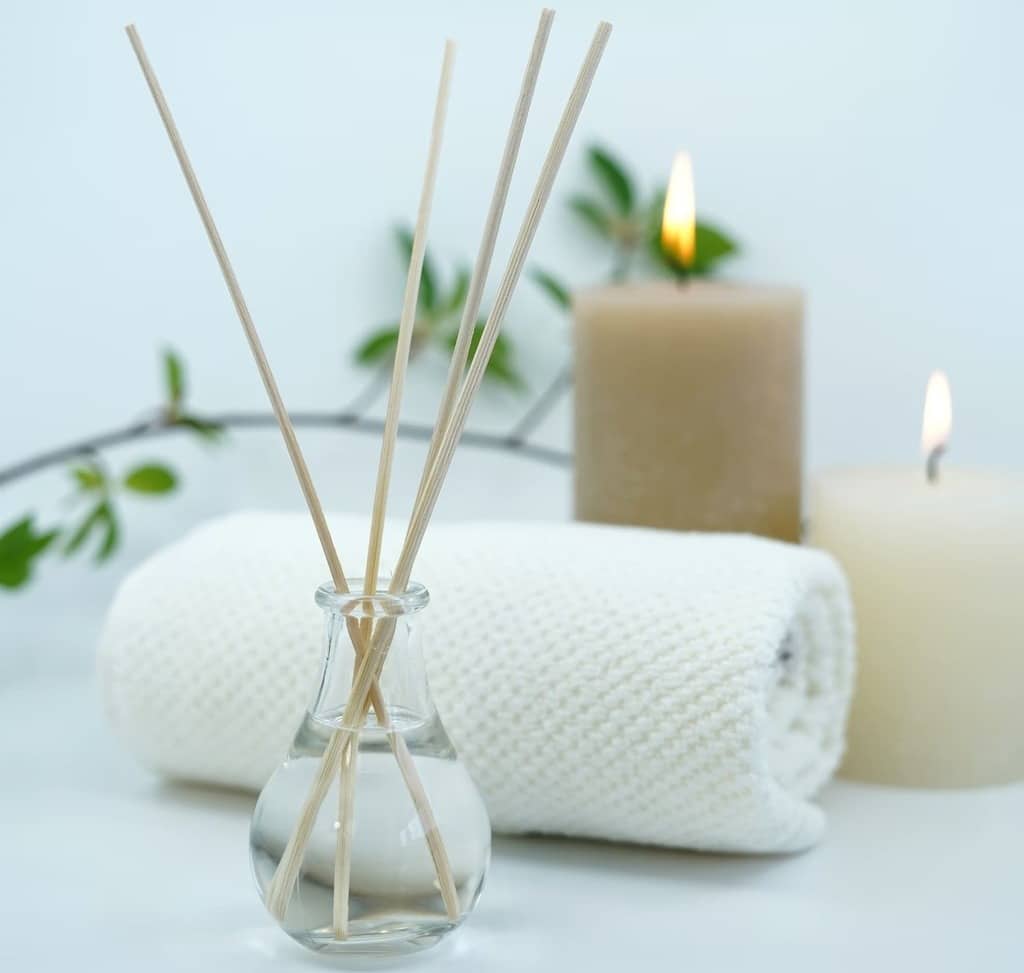
The registration steps for room fragrance are quite similar to those previously discussed. Here’s a detailed look at each step and the corresponding lead times:
- MSDS Creation: Based on the composition of the room fragrance, we create an MSDS. This step takes approximately 10 business days.
- Label Advice: We provide advice on labels in accordance with the CLP, using the created MSDS as a guide. The lead time for this is 5 business days.
- Optional UFI Number Creation: If required, we can create a UFI number, and this process takes about 3 business days.
- Notification to Poison Notification Centers: The final step involves notifying the poison notification centres about the room fragrance, which typically takes 5 business days.
Documents Needed for Each Step
- Formula: For a finished product made with a unique fragrance, its MSDS is required.
- MSDS of Components: In case the MSDS of the finished product is developed from scratch, the MSDS of the components and the fragrance are needed.
- Market and Net Content Information: Details about the countries where the product will be placed and its relative net content are necessary.
- UFI Number: This is needed if we are not handling its creation.
Ensuring Compliance and Peace of Mind During Inspections
To protect against sanctions and ensure tranquillity during inspections by competent authorities, it’s crucial to have all aspects of your product in legal compliance and maintain control over the entire process. Our advice for companies is to conduct a thorough evaluation of the composition, labelling, and information material of the products before they are marketed. This is essential not only for consumer safety but also to avoid hefty penalties. Taobé offers comprehensive support to ensure your product is fully compliant with legislation in all respects. We invite you to contact us for assistance in registering your candles or room fragrances, and we’ll be glad to help!