When developing a cosmetic product, it’s crucial to ensure its long-term stability. To accomplish this, it’s important to answer crucial questions such as how long the product can last on shelves, container compatibility with the formula, and ideal storage conditions.
To answer these questions, a stability test for cosmetic products must be conducted. Stability testing cosmetics involves subjecting the product to a series of tests for a specific duration to verify its continued suitability and safety for sale.
What are the requirements for conducting a stability test, and how long should it take? Moreover, how do you interpret the results of a stability test? In this article, we’ll answer these questions and provide clear guidelines for conducting a valid stability test.
You might also be interested in our article on regulations for cosmetic product labelling.
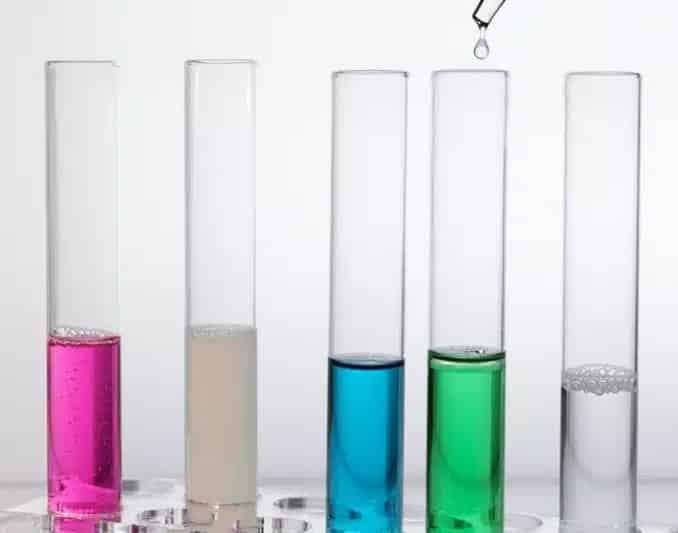
What is Stability Testing in cosmetics?
A stable cosmetic product maintains its characteristics from the date of manufacture for a defined period without undergoing changes or chemical reactions. Stability testing cosmetics is a program designed to detect such changes and reactions by storing samples of the product under specific temperature and humidity conditions.
During stability testing of cosmetics, the product’s characteristics are evaluated over time to determine if it remains stable for the suggested shelf life. This testing allows for the determination of the following:
- Whether the product is stable or not
- If there are any interactions between the ingredients, ensuring they are suitable and compatible with each other without reacting
- The storage conditions necessary to prevent unwanted changes over time to the formula and vice versa, and that the packaging adequately protects the formula from light and the environment
- The shelf life, which estimates how long the product will last on shelves before being suitable for use
- The shelf life is crucial in determining whether to place an expiration date or a period after opening (PAO) on the product label.
The shelf life granted to a cosmetic product is a particularly important piece of information as it determines whether to place an expiration date or a period after opening (PAO) on the product’s labelling.
What is a Compatibility Test in cosmetics?
A Compatibility Test is performed to check the compatibility between a cosmetic product’s formula and its final packaging or container over time. This test verifies whether the ingredients in the product are compatible with the packaging materials. It is a crucial part of the process in the Stability Testing of cosmetics.
During a Compatibility Test, the following phenomena could occur:
- Leakage
- Changes in product or packaging characteristics such as appearance, colour, odour, pH, etc.
- Changes in the packaging integrity
- Signs of corrosion
It is recommended that the compatibility test is conducted at the same time as the stability test to save time. The samples need to be tested once they are in their final packaging, and this needs to be monitored separately to make sure that it does not break, leak, or alter the product’s appearance.

Which products need to be tested for stability and compatibility?
All cosmetic products, regardless of their formulation or packaging, must undergo stability tests to ensure they remain stable in the long term. Stability testing cosmetics or makeup products is a critical component of Good Manufacturing Practices in the cosmetic industry and must be performed during product development. It is also essential to prepare the Cosmetic Product Safety Report required by the EU Cosmetics Regulation (EC) 1223/2009. Safety assessors review stability testing results to determine a product’s safety.
Ensuring that a cosmetic product remains safe and unchanged during its life cycle is crucial to building consumer loyalty and a good reputation for your brand. Therefore, an effective, well-made, and safe cosmetic product is essential for brand success.
What are the requirements to perform a Stability/Compatibility Test?
Firstly, a “proposed shelf life” needs to be established. This is the period during which the product is expected to remain effective, safe, and maintain its characteristics
Once the proposed shelf life is established, samples of the cosmetic product in their final packaging must be stored and incubated under different temperature and humidity conditions.
Several types of Stability Tests for cosmetic products are available based on these conditions. However, a product must undergo at least the following:
How to stability test a cosmetic formula
Real-time or Long-term Stability Testing in Cosmetics
Real-time stability tests for cosmetic products is conducted throughout the proposed shelf life of a product. For instance, if a product has a 2-year shelf life, the real-time stability test should last for 2 years to ensure that the product remains stable throughout this period. This test is comprehensive and reliable, making it the best method for determining a product’s shelf life.
Cosmetic product stability testing guidelines
Long-term stability testing must be performed for cosmetics that will be marketed in different regions, taking into account the temperature and relative humidity conditions in those regions. These tests are conducted under normal conditions (ambient temperature), following the climatic zones established by the ICH guidelines. For example, cosmetic products intended for the European Union and the United Kingdom should generally be tested under climatic zone II (25 ºC and 60% relative humidity).
Climatic Zone | Type of Climate | Temperature | Relative Humidity |
I | Temperate | 21ºC ± 2ºC | 45% ± 5% |
II | Mediterranean / Subtropical | 25ºC ± 2ºC | 60% ± 5% |
III | Hot and Dry | 30ºC ± 2ºC | 35% ± 5% |
IV/a | Hot and Humid / Tropical | 30ºC ± 2ºC | 65% ± 5% |
IV/b | Hot / Higher Humidity | 30ºC ± 2ºC | 75% ± 5% |
Accelerated stability testing COSMETICS and shelf life calculation
Accelerated Stability Testing in Cosmetics
Accelerated stability testing of cosmetics is conducted under high-temperature conditions to accelerate the chemical reactions that may degrade a cosmetic product, predicting how it will behave in the long term. Due to the accelerated degradation process, it is not necessary to carry out the test for the entire proposed shelf life. However, it is recommended that it is conducted for at least 3 months. In the case of the European Union and United Kingdom, these tests are typically conducted at 40-45ºC and 75% relative humidity.
It is essential to note that an accelerated stability test must always be complemented by a long-term stability test. This combination of tests ensures a comprehensive evaluation of a cosmetic product’s stability and safety over its proposed shelf life. By following established guidelines and conducting these tests, manufacturers can develop high-quality and safe cosmetic products that meet regulatory standards and consumer expectations.
Reduced temperature testing
Reduced temperature testing is conducted at low temperatures to establish a reference product, or a “blank”, for comparison with samples stored under long term and accelerated conditions. Products stored at low temperatures change at a slow rate, making them a reliable reference. Additionally, this test can provide data on the behavior of your cosmetic product at low temperatures. The duration of this test should be as long as the long term stability test.

WHICH TESTS ARE SUITABLE FOR YOUR PRODUCTS?
The type of tests required for a product depends on its characteristics. Please contact Taobé for advice on the tests that need to be carried out based on the type of your products. In general, the parameters to check for stability testing cosmetics are the same as those checked to release a product for sale (detailed on the product’s technical data sheet or certificate of analysis), with additional parameters to check the product’s compatibility with the packaging (such as % weight loss, appearance and integrity, visible leakage, etc.).
How to calculate Shelf Life?
Accelerated stability testing cosmetics can increase the degradation process of a product by 2 to 3 times for every 10ºC increase in temperature. If a cosmetic product is stable for 12 weeks (3 months) at 40ºC-45ºC, it can be concluded that the product will remain stable for at least 24 months (2 years). This conclusion should always be supported by the result of a long-term stability test.
WhAT PARAMETERS SHOULD BE INCLUDED IN A STABILITY TEST REPORT?
The stability test report should be comprehensive, including as many parameters as possible. However, at a minimum, the report should include the following information:
- Name of the Cosmetic Product
- Batch tested
- Test start date
- Packaging description and materials
- Type of Stability Test and testing conditions (temperature and relative humidity)
- Details of the tests carried out for the established period, specifying the required specifications
- Results
- Conclusion, which should state the shelf life granted to the product based on the results.
SHOULD STABILITY TESTS for cosmetic products BE PERFORMED BY AN INDEPENDENT LAB OR CAN THEY BE DONE IN-HOUSE?
Stability testing cosmetics or makeup products can be performed in-house if you have a well-equipped lab with all the necessary equipment to carry out the tests. If you don’t have a lab, you can always outsource stability testing.
PAO SYMBOL OR HOURGLASS SYMBOL?
Stability testing cosmetics can also determine the shelf life of a product, which is the time during which the product can remain on a shelf and still be good for consumption. To determine which symbol to use on the product, you will need to follow this rule:
- If the shelf life is less than 30 months: use the hourglass symbol + “Best before” + expiry date.
- If the shelf life is greater than 30 months: use the PAO symbol with a number of months inside the symbol.
Once the symbol is determined, calculate the period of time during which the product remains good for consumption after it has been opened:
- If the hourglass symbol is used, print the expiry date on the packaging at the time of production, based on the shelf life determined by stability testing. For example, if the real-time stability test determined a shelf life of 6 months, the expiry date should be within 6 months from the production date.
- If the PAO symbol is used, determine the number of months to write inside the symbol based on the stability test results and the guidelines recommended by Afssaps.
STILL HAVE QUESTIONS ABOUT STABILITY TESTS?
At Taobé, we can provide advice on every aspect of your stability testing program. If you have any questions or need help, please do not hesitate to contact us.
See also our guide on regulatory compliance to get a better understanding of what is necessary to be compliant in Europe and the UK.