What are “CLP products”?
“CLP products” are chemical products that must comply with Regulation (EC) No. 1272/2008. This regulation, introduced in the EU in 2009, is based on the United Nations’ Globally Harmonised System (GHS) and aims to standardise the classification, labelling and packaging of chemicals and hazard information globally.
The Objectives of the CLP Regulation
CLP requires all chemicals to be:
1. Classified: Chemical substances and mixtures must be classified according to their risks, such as toxicity, corrosivity, flammability, etc.
2. Labelled: They must have labels with hazard symbols (pictograms), risk phrases, and precautionary statements that clearly inform users about the dangers of the product.
3. Securely packed: Packaging should ensure safety during transport, use, and storage, with specific features such as child safety locks where necessary.
Pictograms and Risk Phrases
Products that fall under the CLP regulation must bear specific hazard pictograms, such as skulls for toxic substances or flames for flammable products. The H-phrases (Hazard) describe the hazards, while the P-phrases (Precautionary) provide precautionary advice for the safe use of the product.
Scope
The CLP regulation applies to all chemicals and mixtures used in industrial and domestic environments, such as detergents, paints, pesticides, etc. However, some industries, such as pharmaceuticals and food, have specific regulations that override CLP in certain respects.
In summary, CLP is essential for ensuring chemical safety and clear communication of health and environmental risks, while also supporting the safe trade of chemicals within the EU and globally.
What Are the Registration Steps of a CLP Product
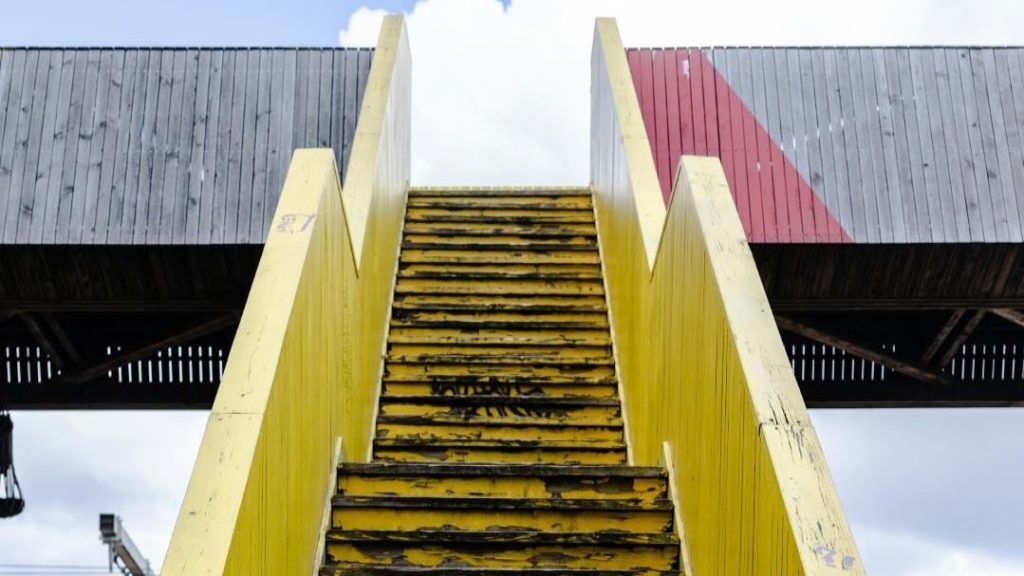
To register a chemical product under the CLP (Classification, Labelling and Packaging) Regulation in the European Union, a specific process must be followed. Below is an overview of the main steps:
1. Identification of the Substance or Mixture
– Verification of the chemical characteristics and composition of the product to define its identity.
– If your substance is already registered in the European Chemicals Agency (ECHA) database, you can use your existing identification.
2. Classification of the Substance or Mixture
– Determination of classification according to CLP criteria, based on experimental evidence, scientific data, and guidelines provided by the regulation.
– Identification of hazards to human health, safety and the environment (e.g., flammability, toxicity, carcinogenic and/or mutagenic effects).
3. Product Labelling
– Creation of the label in compliance with the CLP regulation, with all the mandatory elements:
– Hazard pictograms: Graphic symbols that indicate the types of risk (e.g. flame, skull).
– Hazard statements (H): Hazard descriptive phrases (e.g., “Causes serious eye damage”).
– Precautionary statements (P): Phrases that suggest precautions for use (e.g. “Wear protective gloves”).
– Identification data: Name and address of the manufacturer or importer, quantity of the product, etc.
4. Compliant Packaging
– Make sure the packaging is secure and suitable, with any safety fasteners and devices for visually impaired people (such as any tactical pads).
5. Notification to the ECHA Database
– The notification of classification and labelling must be sent to the ECHA database, a mandatory step for all chemicals placed on the European market.
– You must submit a Safety Data Sheet (SDS) for hazardous substances or mixtures, which contains detailed information on handling and first aid measures, in accordance with REACH and its annexes.
6. Continuous Updating and Renewal
– Monitoring for any new scientific or regulatory information that may require an update in classification, labelling, or packaging.
– If new data on the risks or use of the substance emerges, both the notification and the labelling must be updated.
7. REACH compliance (if applicable)
– For many substances, the CLP Regulation is supplemented by REACH 1907/2006 (Registration, Evaluation, Authorisation and Restriction of Chemicals), which requires a more detailed registration if the substance is manufactured or imported in quantities exceeding one tonne per year.
Specifically, REACH sets out the general requirements for the creation of SDSs, as described in point 5. It requires that each hazardous chemical substance or mixture be accompanied by a safety data sheet that includes details of the health and safety risks.
The structure and content of the SDS must follow the requirements set out in its Annex II (now amended by Regulation 878/2020), which specifies the 16 mandatory sections of the SDS, as identified by guidelines from the European Chemicals Agency (ECHA).
These steps are mandatory to ensure that the product is safe for consumption and industrial use and to ensure proper risk communication to end users and workers.
Detailed Guide: SDS for the Finished Product or Fragrance?
Safety Data Sheets (SDS) are mandatory documents for hazardous chemicals, ensuring that everyone involved in handling, transport, and use has complete information on risks and precautions.
Below is the process for creating an SDS according to regulations such as REACH and CLP:
1. Collection of Information on the Substance or Mixture
– Product Identification: Trade name, chemical formula, Chemical Abstracts Service (CAS) number, and other identifiers.
– Hazard Classification: Information collected from risk assessments and hazard tests (toxicity, flammability, environmental effects, etc.), also used to determine CLP classification.
– Composition: Details of the chemical ingredients present in the mixture and their percentages, to allow a correct risk assessment.
2. Organization of Information in the 16 Mandatory Sections
Each SDS must follow a standard structure of 16 sections, each providing specific information.
Here is a summary:
1. Product and Company Identification: Name, intended uses, and contact information of the manufacturer or importer.
2. Hazard Identification: Physical, health and environmental hazards according to the CLP classification.
3. Composition/Ingredient Information: Chemical components, percentages and CAS numbers.
4. First Aid Measures: Actions in the event of exposure or accident.
5. Fire Fighting Measures: Recommended Fire Extinguishers and Firefighting Methods.
6. Accidental Release Measures: Actions to be taken to stem any leaks.
7. Handling and Storage: Precautions and conditions for safe use.
8. Exposure Control/Personal Protection: PPE (Personal Protective Equipment) and exposure limits.
9. Physical and Chemical Properties: Physical state, colour, odour, boiling point, pH, etc.
10. Stability and Reactivity: Chemical stability and conditions to be avoided.
11. Toxicological Information: Short and long-term effects, acute toxicity, sensitization, etc.
12. Ecological Information: Environmental impact of the substance or mixture.
13. Disposal Considerations: Safe Disposal and Recycling.
14. Transport Information: Risk Classes, Labels and UN Number.
15. Regulatory Information: Product-specific legislation, including local regulations.
16. Other Information: For example, an explanation of the abbreviations used.
3. Drafting and Formatting of the SDS
– Each section must be completed following the rules of the two aforementioned REACH and CLP regulations, with clear and precise language to allow anyone handling the product to understand.
– Technical data must come from reliable sources, such as chemical databases, scientific studies, and certified laboratory tests.
4. Periodic updating of the SDS
– An SDS should be updated whenever there is new information on the risks of the product or changes in regulations.
– The update should be communicated to all previous recipients of the SDS to ensure continued security.
In summary, the creation of an SDS is a structured and regulated process, which requires accuracy and regulatory compliance to ensure the safety of those who use and handle the chemicals, including the fragrance that constitutes the finished product.
Compliance Formula
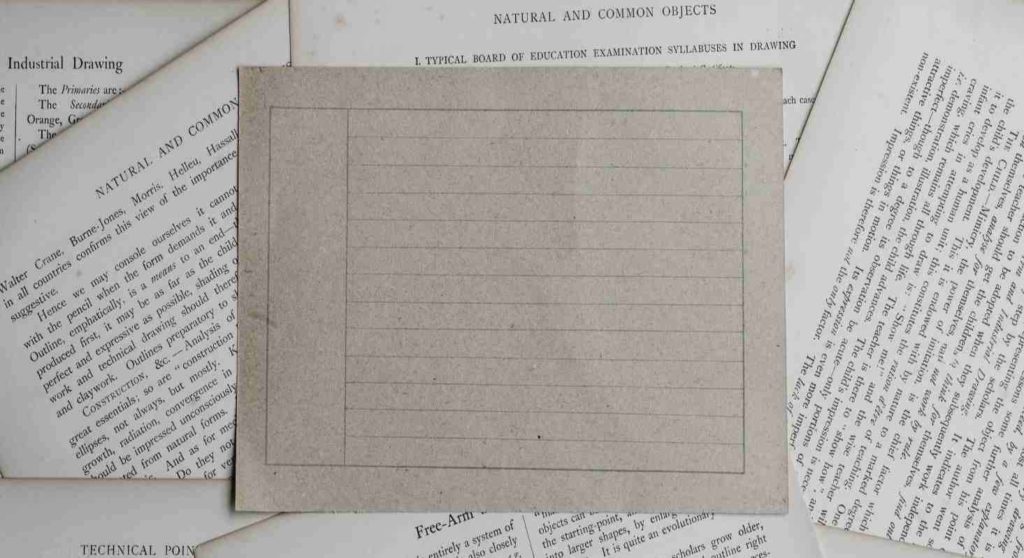
1. Classification of Formula Constituents
- Component identification: Verification of each substance present in the formula, including any additives or impurities.
- Consult the databases: For the classification of chemical components, consult the ECHA database or other regulatory resources such as the REACH register of registered substances. Here you can find information on the classification of each ingredient according to CLP criteria.
- Internal classification: If the formula includes new ingredients or undocumented concentrations, testing may need to be conducted to determine its internal classification.
2. Verification of Concentration Limits
- Comparison of the concentration levels of each component with the exposure limits and concentration limits set by the REACH and CLP regulations for hazardous substances.
- Consequently, it verifies that the percentages of the components are within the permitted limits for each hazard class. Some chemicals have specific concentration limits that, if exceeded, require a different classification and updated hazard labelling.
Label Check
1. CLP labelling: Check that the product label complies with CLP requirements, with hazard pictograms, H (Hazard) and P (Precautionary) phrases, and appropriate hazard statements.
2. SDS compliant with 2020/878: Verifies that the SDS contains all the required information, updated according to the aforementioned Regulation 2020/878, such as indications on endocrine disruptors, nanoforms, and exposure scenarios (if necessary).
PCN Notification
The Poison Centres Notification (PCN) is a notification system for poison centres in the European Union, managed by the European Chemicals Agency (ECHA). It was established to improve consumer and worker safety by ensuring that information on hazardous chemicals is readily available to poison control centres.
PCN notification is mandatory for all suppliers of hazardous mixtures classified according to the CLP Regulation and made available to the public or for professional use in the EU.
The reference article of the Rules of Procedure is Article 45. If, on the other hand:
- you manufacture the substance and it is subject to registration under REACH; or
- you import the substance and it is subject to registration under REACH; or
- the substance is manufactured or imported and it is classified as hazardous, regardless of the quantity; or
- a mixture containing the substance that is classified as hazardous and is present in quantities above the relevant concentration limit is imported, resulting in the mixture being classified as hazardous under CLP; or
- import an article containing substances that are subject to registration under Article 7 of the REACH Regulation.
Then it is necessary to notify ECHA, within one month of placing on the market, the information listed in Art. 40 CLP (C&L notification).
Here are the main activities to be carried out on the PCN portal:
1. Preparation of the Notification
– Gathering the necessary information: For each hazardous chemical, you need to collect essential data, including:
– Detailed formula and composition of the mixture: with concentrations and chemical identity of each component.
– Data on intended use: description of uses (domestic, professional, industrial).
– Labelling information: according to CLP classification, including risk phrases (H-phrases) and precautionary statements (P-phrases).
– UFI Code (Unique Formula Identifier): Create a UFI code, a unique identifier of 16 characters for each mixture, which must be reported on the label of the dangerous product. More on that later.
2. Creating and Sending the Notification on the PCN Portal
– Portal access: If you don’t have an active account, you’ll need to register and set up an account in order to proceed with notifications.
– Filling in the notification: Entering the mixture data using the harmonised standard format (XML or IUCLID) to ensure that the information is compatible with the PCN system.
– Uploading documentation: Providing SDS (Safety Data Sheets), additional information, and subsequent uploading of required documents, such as labelling.
3. Verification and Confirmation of Compliance
– Notification control: Once the entry is complete, the system allows you to review the information to ensure that it is accurate and compliant with the requirements.
– Send and confirm: After review, you can send the notification. The PCN system will confirm receipt and provide a reference number, which is useful for any updates or to track the notification.
4. Notification Updates
– Changes to the formula or label: If there are any changes to the composition of the mixture, its classification, or intended use, the PCN notification should be updated to ensure that poison centres have up-to-date information.
– Periodic reviews: Based on regulations and updates to CLP or REACH, it is advisable to perform periodic audits to maintain compliance.
Scope of PCN Notification
The PCN system covers all mixtures classified as hazardous under the CLP Regulation, including paints, detergents, household and industrial chemicals, as long as they are made available to the public or for professional use.
PCN Requirements Across Different European Market Countries
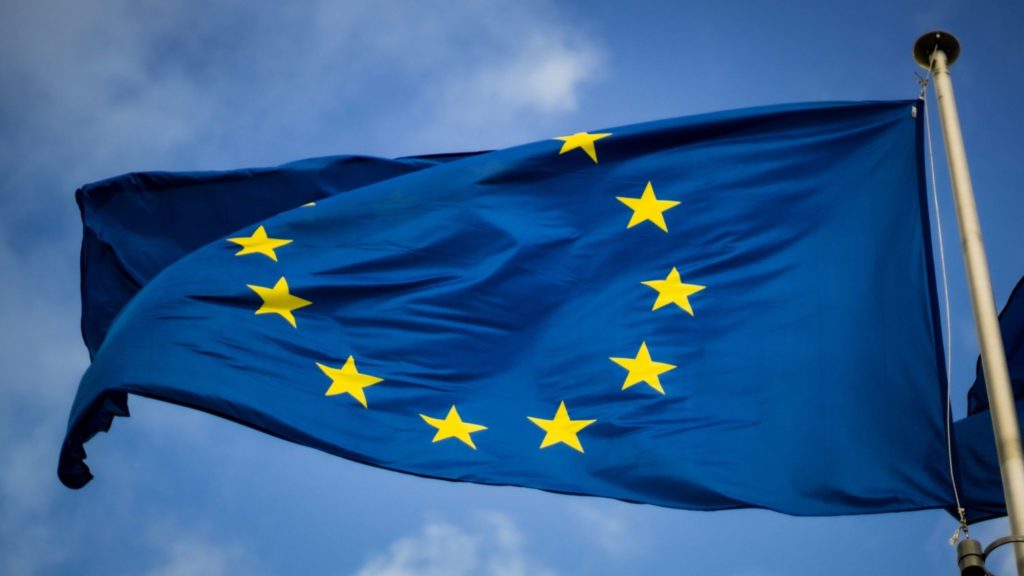
The requirements of the PCN are harmonised across all EU member countries, but each member state retains a degree of autonomy in implementation. While general notification requirements are similar, national differences may affect the notification process.
Key areas where requirements may vary include:
1. Language of the Notification
– Each Member State may require that the notification and information (such as the SDS) be presented in the official language of the country. For example, if you are notifying a product in Italy, the notification and associated information may need to be provided in Italian (although, in this case, English is accepted).
2. Fees and Costs of the Notification
– Some Member States charge fees for handling the notification, while others offer the service free of charge. Rates, if any, can vary significantly from country to country.
3. Request for Additional Information
– Some Member States may require additional information beyond what is required by the EU harmonised format, such as details on certain substances contained in the mixture or specific environmental information.
4. Notification Timelines
– The deadline for PCN notifications is harmonised for most mixtures, but some countries may have different requirements for specific categories of mixtures or for products already on the market before the current rules come into force.
In summary
To ensure that the notification is compliant in each Member State where the product is marketed, it is important to:
- Check the language requirements and any requests for additional portals.
- Ensure that labels and SDSs comply with specific national requirements.
- Consult national authorities or an expert adviser for any applicable exceptions or variations.
Understanding the UFI Code
The UFI (Unique Formula Identifier) is a unique 16-character code introduced by the European Union’s CLP Regulation to clearly and accurately identify the composition of hazardous mixtures. It was created to help poison control centres provide timely and correct information in the event of an emergency, making it easier to identify the product and its characteristics.
Structure of the UFI
– The UFI is composed of a combination of letters and numbers arranged in four blocks (e.g. YV1T-5CN4-A00Y-FR7J).
– It is automatically generated using the company’s tax code and a specific coding of the mixture formula (decided by the company itself, usually progressive), making it unique for each formulation and for each company.
Where it Should Be Applied
– The UFI must be printed on the label of the dangerous product, in a clear and visible way.
– It must be accompanied by the words “UFI:” followed by the code itself.
– For industrial products, the UFI can be reported in the Safety Data Sheet (SDS) instead of on the label.
How to Generate a UFI
1. Access the UFI Generator on the ECHA website: here you can enter the tax code and a combination of numbers that represents the formula of the mixture.
2. Code generation: the tool calculates the UFI code, which will be unique to that mixture.
3. Upgrades: Whenever the composition of the mixture changes, a new UFI may need to be generated.
Notification Obligations
The UFI must be included in the Poison Centres Notification (PCN) and registered in ECHA’s PCN portal to be communicated to the poison centres in the EU countries where the product will be distributed.
In summary, the UFI represents a standardised and harmonised identification system in the EU that facilitates the rapid and appropriate intervention of poison centres in the event of accidental exposure or accident.
A Final Word On MiM (Mixture in Mixture)
MiMs (Blends in Blends) refer to pre-formulated blends that are used as ingredients to create other blends. This term is very common in the chemical industry and describes a situation where a manufacturer uses an existing mixture as a component to produce a new mixture.
MiMs are widely used, for example, in the production of paints, detergents, cosmetics and other chemicals.
MiM Characteristics
– Pre-mixed: MiMs are pre-formed mixtures, with a specific composition and classification, which are purchased or prepared and then introduced into a new mixture.
– Multipurpose components: Often, the same MiM can be used as an ingredient in different final formulations.
– SDS of the MiM: The MiM has (should have) its own Safety Data Sheet (SDS), which contains information on classification, chemical properties and risks.
Regulation and Classification of MiM
When a MiM is used to produce a new mixture, it is important to:
1. Know the composition and classification of the MiM: The SDS of the MiM provides details on the composition and hazardous properties, which must be considered in the final classification of the new mixture.
2. Apply the UFI Code to the MiM, if hazardous: Since every hazardous mixture requires a UFI, a hazardous MiM must also have its own UFI code, which will be shown on the label of the final mixture.
3. Calculate the Final Mixture Classification: The final classification of the mixture must take into account the hazard of the MiM, applying the criteria of the CLP Regulation.
PCN notification for MiMs
– When creating a mixture that contains a MiM, you can use the information from the MiM itself to complete the PCN notification. However, the manufacturer of the final mixture is responsible for making sure that the notification includes all relevant risk information and safety measures.
– If the MiM has been previously notified to the PCN by a supplier, you can use the details already recorded, but notification of the final mixture is still required.
Essentially, MiMs simplify the manufacturing process by allowing pre-formulated ingredients to be used. However, they require attention to ensure that all safety information, classification, and notifications are properly transferred and considered in the final blend.
Conclusion
There are many obligations and requirements to comply with the aforementioned reference regulations. Contact us to make sure your product is never stopped at customs or seized!